Plastic Pipe Caps and Plugs: The Key To Preventing Contamination in Pipes
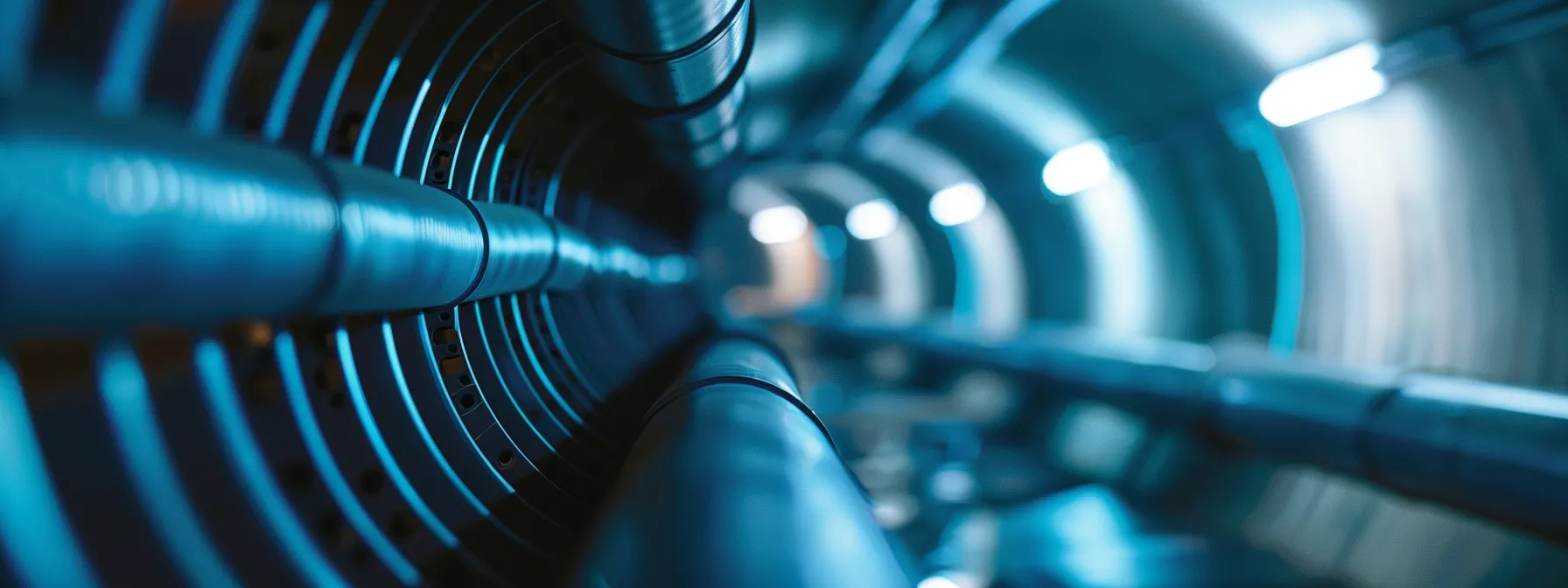
In the realm of industrial maintenance and safety, safeguarding pipes against contaminants is a critical task often overshadowed by more direct operational concerns. However, ensuring that pipelines remain uncontaminated is essential for system longevity, product purity, and overall safety. Plastic pipe caps and plugs serve as simple yet indispensable tools in this effort, effectively sealing off pipe ends and openings from environmental factors and debris. They are designed not only to protect pipes during storage and transit but also to maintain the integrity of the fluid or gas that passes through them. Below we will explore the nuances of these protective accessories and delve into why they are so crucial for success in various industries.
Understanding Plastic Pipe Caps and Plugs and Their Importance in Pipe Maintenance
Plastic pipe caps and plugs are essential for securing the ends of pipes and tubes, providing a barrier against external elements. They are particularly useful in industries with extensive pipe networks, as open pipes can be a gateway for dust, moisture, pests, and pollutants, leading to corrosion, product contamination, and system failure. Prevention is crucial to avoid costly cleaning, repair, or replacement costs.
These caps and plugs ensure worker safety by preventing accidental exposure to hazardous materials within the pipeline. Plastic variants are preferred due to their versatility, cost-effectiveness, and ease of use in diverse environmental conditions. Ensuring the correct size and type of cap or plug is crucial for optimal protection. Mismatches can lead to loose fittings, while overly tight fittings may cause damage or difficulty in accessing the pipe.
Material Selection for Plastic Pipe Caps and Plugs: Advantages and Considerations
Pipe caps and plugs are made from various plastics, each offering varying levels of protection and adaptability. Polyethylene is widely used due to its durability, flexibility, and chemical resistance. For industries requiring extreme conditions, materials like PVDF or PTFE are often chosen due to their superior resistance properties.
Environmental considerations are also influencing material selection, with biodegradable plastics becoming more popular for companies seeking to reduce their environmental footprint. Cost-effectiveness is another factor to consider, as advanced plastics may offer superior protection but also come at a higher price point. A balance must be found between affordability and the required level of protection for each application.
The Role of Pipe Caps and Plugs in Contamination Prevention and Pipe Integrity
Plastic cap plugs play a vital role in protecting pipes from contaminants that can damage both the pipes and the substances they carry. By sealing off the ends of unused pipes or those in transit, they keep internal environments clean and safe from intrusion, ensuring the integrity of the system.
In industries like pharmaceuticals or semiconductors, even the smallest contaminants can cause significant problems. Reliable plastic cap plugs help maintain strict cleanliness standards, while in outdoor settings like construction or oil fields, they shield pipes from mud, water, and other harmful elements.
Installation Best Practices for Effective Sealing and Contamination Control
Proper installation of pipe caps and plugs is crucial for their effectiveness. They should fit snugly against the pipe, creating a seal to prevent contaminants. It’s important to avoid damaging the pipe and compromising the seal. Clean surfaces of both pipes and the caps are essential for optimal performance.
Consistent pressure and avoiding excessive force are crucial for proper installation. Automatic or semi-automatic cap and plug installers can streamline the process and reduce human error. Regular inspections are essential to ensure the cap or plug remains intact and properly positioned. Regular checks can detect and address issues before they escalate into larger problems.
Real-World Applications and Success Stories in Industrial Settings
Plastic pipe caps and plugs have proven to be crucial in industrial settings, saving companies from costly downtimes and product spoilage. In the oil and gas industry, they have been instrumental in protecting drilling equipment during transport and storage, reducing sand and water intrusion, and enhancing operational reliability. In the automotive sector, plastic pipe caps and plugs are used during painting and coating processes, protecting engine and exhaust components and minimizing paint contamination.
In water treatment facilities, a comprehensive pipe protection strategy involving caps and plugs has led to a significant decrease in system contamination incidents, boosting public confidence in safe water provision. The use of plastic pipe caps and plugs is essential for maintaining a clean and safe environment in various industries.
Altogether, the incorporation of plastic pipe caps and plugs into maintenance and storage protocols demonstrates a proactive approach to protecting critical infrastructure. The small investment in these components can yield substantial returns in reliability and safety. They represent an essential tool in the modern industrial landscape, preventing contamination and preserving the efficacy of piping systems around the globe.